Mkniemy co koń wyskoczy na naszych stalowych rumakach w kierunku Asolo. To właśnie tam, gdzie Alpy zamieniają się w żyzne doliny pełne winnic i uprawnych pól, mamy spotkanie z dwoma osobami odpowiedzialnymi za kolekcję butów narciarskich firmy Dalbello. Droga ze szwajcarskiej Lenzerheide wiedzie przez trzy przełęcze: Albula, Offen i Gampen, co umożliwia łączenie przyjemnego z pożytecznym. Słońce świeci, motocykle warczą, widoki zapierają dech w piersiach. Fajnie jest.
Po minięciu Trydentu pędzimy dalej doliną rzeki Brenta. Co i rusz mijamy tablice wskazujące drogę do kolejnych stacji narciarskich: Paganella, San Martino di Castrozza, Passo Rolle… Pomału zostawiamy góry po lewej stronie i wjeżdżamy w najeżony willami i winnicami rejon alpejskiego przedgórza. Wreszcie docieramy do Asolo, gdzie wille patrycjuszy przeplatają się z fabrykami sprzętu sportowego, maszyn i odzieży. Samo miasteczko zachowało dawny kształt i charakter z wąskimi, pięknymi, zacienionymi uliczkami. Na wzgórzu ponad miastem rozłożył się potężny niegdyś zamek. Senna atmosfera miasteczka bardzo kontrastuje ze wszystkim, co dzieje się poniżej, w dolinie. To istne zagłębie przemysłu sportowego. Oprócz Dalbello są tu także fabryki firm, takich jak Scarpa, Alpinestar, Gaerne, a w nieodległej Montebellunie (zaledwie 9 km) swoje siedziby mają m.in. Lange, Nordica, Tecnica i Head.
Tajemnice w tym rejonie nie istnieją
– mówi Ivan Santin, który oprowadza nas po okolicy, a na co dzień jest product managerem Dalbello.
Nikt tego nigdy nie przyzna, ale w rzeczywistości tak jest. Mam wielu znajomych czy nawet przyjaciół, którzy pracują dla innych firm i często rozmawiamy o naszych zajęciach, no bo niby o czym innym? Nie możemy po prostu omijać pewnych tematów. Okolice Asolo użytkowane są od bardzo dawna. Ze względu na wspaniały klimat bardzo wiele bogatych rodzin weneckich miało tu swoje letnie rezydencje. Wiecie, wenecka laguna w gorące lato śmierdziała jak kloaka. Tu u podnóża Alp było znacznie przyjemniej. To dlatego, gdziekolwiek by człowiek spojrzał, w polu widzenia będzie jakaś patrycjuszowska willa z otaczającą ją winnicą. Drewno z okolicznych lasów stanowiło też materiał na pale wbite w morskie dno, na których zbudowana jest Wenecja. Dziś w okolicy jest mnóstwo przemysłu, a jednym z większych przedsiębiorstw regionu jest nasze.
Wracamy do firmy. Nowy budynek biurowy Dalbello z jednej strony graniczy z halą produkcyjną, a z drugiej z domem, w którym Alessandro Dal Bello od 1960 r. produkował buty narciarskie. Historię firmy przedstawialiśmy kilka sezonów temu, więc teraz skoncentrujemy się jedynie na rzeczach najważniejszych. Alessandro Dal Bello był typowym przedstawicielem emigracji zarobkowej. W latach 50. ubiegłego stulecia pracował dla istotnej wówczas szwajcarskiej firmy Henke. W 1960 r. wraz z rodziną powrócił do Asolo i rozpoczął produkcję górnych części skórzanych butów dla Henke. Kiedy szwajcarska firma upadła, Dal Bello otrzymał kontrakt na produkcję wkładów do plastikowych już butów narciarskich od kolejnego helweckiego producenta, firmy Raichle. W 1974 r., bazując na doświadczeniach zdobytych przy produkcji dla innych, Dal Bello zdecydował się na stworzenie własnej linii butów. Powstanie marki Dalbello stało się faktem. Kiedy z powodu różnych nieszczęśliwych zbiegów okoliczności Kneissl pociągnął za sobą na dno Raichle, Alessandro Dal Bello miał dwa wyjścia: zająć się czymś innym albo kontynuować produkcję na własną rękę pod własną nazwą i próbować wyrywać dla siebie część trudnego rynku. Na szczęście wybrał drugą opcję. Przez kilka lat firma Dalbello zdobywała rynek, wytwarzając buty dla początkujących i średnio zaawansowanych. Nie zapominano jednak też o produktach z najwyższej półki dla narciarzy ekspertów. Dziś firma – po kolejnych zawirowaniach rynkowych – jest częścią grupy MDV, czyli Marker-Dalbello-Völkl, i jednym z najbardziej liczących się producentów butów narciarskich na świecie.
W firmie, oprócz wspominanego już Ivana Santina, czeka na nas Peter Cagliari, mający tytuł divison managera, zatem obaj panowie to fachowcy w każdym calu. Plan jest prosty: zobaczymy produkcję, zadamy pytania i napiszemy relację. My jednak chcemy więcej. Bardziej interesuje nas proces powstawania nowego modelu butów narciarskich, czyli jak teoria – myśl staje się praktyką – gotowym produktem.
Wiemy też, że skonstruowanie form do wtryskarek, czyli tak zwanych moldów dla jednego modelu, ale we wszystkich rozmiarach, to koszt około 1 mln euro. Trzeba więc wszystko dobrze przemyśleć, zanim zainwestuje się pieniądze. Nasi gospodarze wymieniają spojrzenia i rozpoczyna Peter:
Dziś wszystko jest inaczej, niż było jeszcze nie tak dawno temu. Całkiem niedawno na rynku dominowały trzy typy butów narciarskich. Pierwsze to takie, które w swojej budowie podobne były do Raichle Flexon, gdzie na pierwszym miejscu stawiano bardzo dobre czucie nart i śniegu. Drugie odpowiadały Nordicom Grand Prix, gdzie cholewka była trwale połączona z dolną częścią skorupy, zapewniając bardzo dużą sztywność i błyskawiczne przekazywanie energii. Trzeci typ odpowiadał budowie sportowych butów Lange, w których cholewka i dół połączone były za pomocą zawiasu umożliwiającego bardziej homogeniczny, naturalny flex. Były jeszcze oczywiście i tylnowejściowe, ale ten typ do poważnego narciarstwa nie nadawał się nigdy. Dziś na rynku mamy nieprawdopodobną mnogość specjalistycznych modeli. Są buty wyczynowe, sportowe, rekreacyjne, skitourowe, freetourowe, damskie, dziecięce, juniorskie, superlekkie itd.
Najpierw trzeba więc odpowiedzieć sobie na ważne pytanie, jakiego nowego modelu potrzebujemy? Do tego służy analiza rynku i oczywiście analiza poczynań konkurencji. Żadna firma w branży nie funkcjonuje w próżni i nawet jeśli wymyślimy coś rewolucyjnego, ale kompletnie oderwanego od dotychczasowych rozwiązań, raczej nie odniesiemy sukcesu. Ewolucja musi przebiegać powoli, bo inaczej rynek odrzuci zbyt radykalne zmiany.
Drugi krok to wybór materiału. Możemy wybrać pomiędzy poliestrem, polieterem lub grilamidem. Każdy z materiałów ma swoje zalety, ale także i wady. Dosłownie kilka lat temu świat butów narciarskich zachwycał się nylonem o nazwie grilamid. Byliśmy dość ostrożni w przestawianiu od razu całej produkcji na nowe tworzywo i okazuje się, że było w tym dużo racji. Dziś wiadomo, że grilamid sprawdza się bardzo dobrze w przypadku konstrukcji lekkich, na przykład freetourowych, ale słabo nadaje się do butów sportowych. Po prostu tak sztywny materiał zbyt dobrze przenosi wibracje. Im szybsza jest jazda po twardym stoku, tym słabiej wypada on w porównaniu z bardziej elastycznymi tworzywami.
Kolejny punkt, na który zwracamy uwagę, to tak zwane DNA firmy. Musimy zachować pewną ciągłość produktów, żeby nie zrazić do swoich pomysłów ludzi, którzy już nam zaufali. Analizujemy też zmiany anatomiczne na przestrzeni lat. To bardzo ciekawy problem. Okazuje się, że z powodu powszechnego dostępu do wygodnych butów stopy dzisiejszej młodzieży są dłuższe i szersze od stóp rówieśników jeszcze przed 40 latami.
Bierzemy też pod uwagę wpływ internetu, który jest bardzo ważny. Z jednej strony, nasze produkty muszą być precyzyjne i techniczne, a z drugiej, biorąc pod uwagę, jak wielka część sprzedaży odbywa się przez sieć, powinny pasować na większość klientów out of the box. Jednocześnie jednak opracowujemy całą listę uwag dla bootfitterów. Na przykład: które modele i w jakich strefach można frezować, a które można rozciągać na gorąco i w jakim stopniu.
Pod uwagę bierzemy też fakt, że narciarstwo jest sportem, który się starzeje. W dzisiejszym świecie najwięcej czasu na jazdę na nartach mają emeryci. Młodzież jest mniej zainteresowana tak zwanym realem niż jeszcze kilka lat temu. Kolejny punkt to efektywność inwestycji. Dwie dekady temu jeden model butów pozostawał w ofercie na 10 do 12 lat. Oczywiście w ciągu tego czasu podejmowane były liftingi, jak na przykład zmiana kolorystyki. Dziś żywot jednego modelu to pięć lat. Możemy jeszcze dodać kolejne dwa sezony wykorzystania moldów dla produkcji SMU i koniec…
Kiedy zbierzemy już te wszystkie informacje, powstaje tak zwany brief, czyli założenia produkcyjne, które nasi projektanci za pomocą programów CAD i CAM przenoszą na ekrany komputerów. Jednocześnie opracowujemy dodatki techniczne, czyli: klamry, nity, zawiasy, ewentualne mechanizmy ski-walk itp. Kiedyś taki proces trwał dwa lata lub dłużej. Dziś, dzięki pomocy programów i symulacji komputerowych, jesteśmy w stanie skrócić go do roku lub nawet trochę mniej. Zwykle działamy w ten sposób, że określamy moment, kiedy nowy model powinien pojawić się na rynku, i odliczamy czas do tyłu, decydując o terminie rozpoczęcia prac.
Kiedy w komputerze mamy już gotowy produkt, możemy wykonać tak zwany rapid prototype. To gotowe buty narciarskie, tyle że zrobione na drukarce 3D, a nie we wtryskarce. Oczywiście materiał jest trochę inny, ale za pomocą modeli matematycznych programu CAM możemy wydrukować buty w taki sposób, żeby zgadzała się objętość i rozkład fleksu. Taki prototyp może już być sprawdzony na śniegu. Jak wiecie, do ośrodków górskich daleko nie mamy. Jeśli musimy testować latem, to lodowce też nie są szmat drogi stąd.
Po przetestowaniu prototypu ponownie zbieramy dane od naszego zespołu sprawdzającego, poprawiamy detale i wypuszczamy drugi prototyp. Jeśli wszystko się zgadza, kolejny etap prac należy do budowniczych moldów. To prawdziwi artyści w swoim fachu, przypominają rzeźbiarzy. Najpierw budujemy formę dla jednego rozmiaru i wykonujemy pierwszą małą partię do testów. Głównym atutem naszej firmy jest fakt, że wszystkie elementy plastikowe do produkcji wykonujemy na miejscu w Asolo. Na miejscu szyjemy też wkłady do prototypów. Seryjne wkłady wykonywane są w Bułgarii, gdzie niewielką filię (20 osób) założył jeszcze Alessandro Dal Bello. Kiedy zbierzemy wyniki testów prototypów wykonanych już na wtryskarkach, dokonujemy ostatecznych, niewielkich poprawek i gotowe. Zatwierdzamy model do produkcji i budujemy kolejne moldy dla pozostałych rozmiarów.
Teraz pozostaje jeszcze tylko przeprowadzenie właściwego marketingu nowego modelu, a to w dzisiejszych czasach wcale takie łatwe nie jest. Z jednej strony, mamy mnogość produktów danego segmentu, a z drugiej, dostęp do informacji jest bardzo szybki i to nie tylko tych pozytywnych. Na przykład influencerzy mogą narobić bardzo dużo złej roboty. Influencer może, bez podania przyczyny, wypowiedzieć się w sposób negatywny o jakimś produkcie i zostanie wysłuchany. Cóż z tego, że nie ma pojęcia o butach narciarskich, skoro ma kilka milionów polubień swoich produkcji.
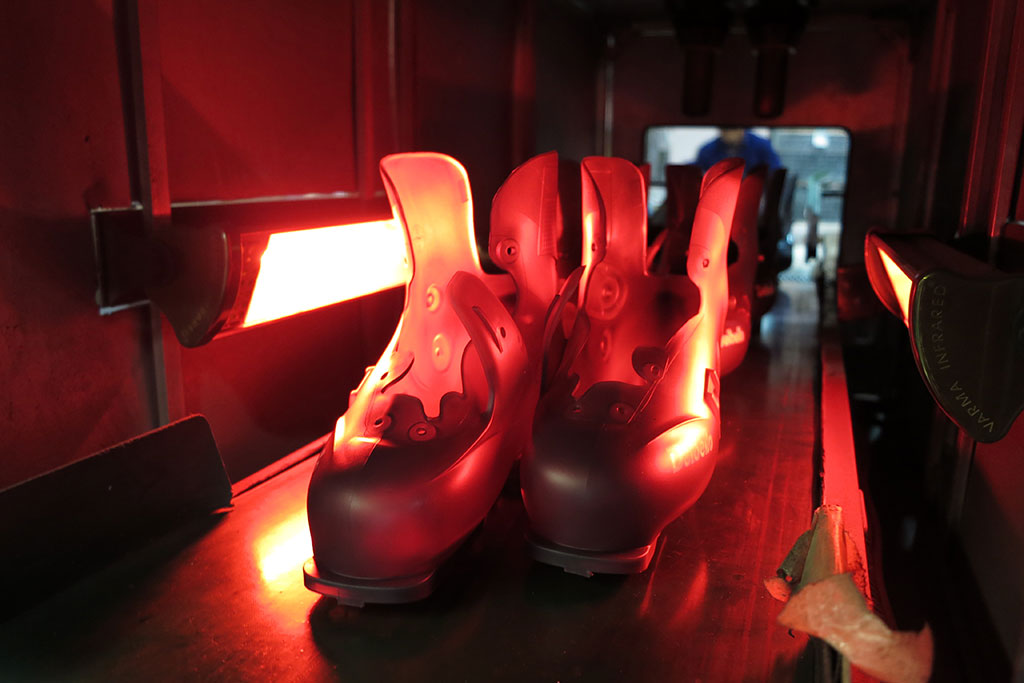
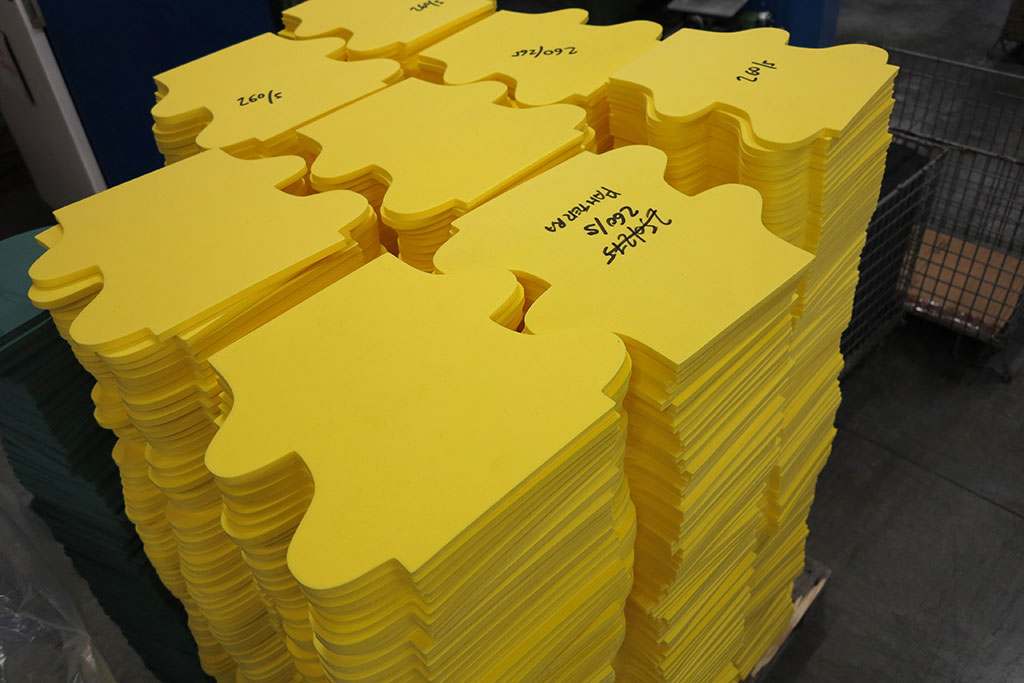
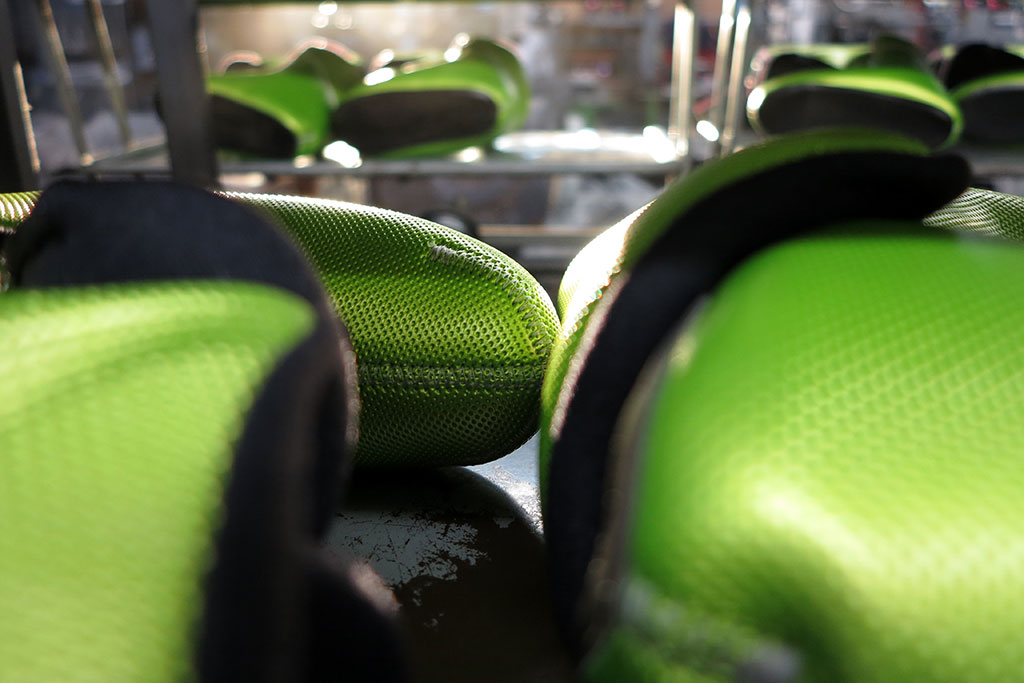
Pytamy jeszcze o przyszłość. Jak według naszych rozmówców będzie wyglądał rynek butów za kilka lat? Obaj są zgodni, że przyszłość to komfort. Coraz mniej ludzi oczekuje na stokach wspaniałych osiągów od swojego sprzętu. Narciarstwo coraz bardziej dryfuje w kierunku aktywności, której uczestnicy chcą po prostu dobrze się zabawić w górach, a prawdziwych pasjonatów będzie coraz mniej. Trochę to smutne dla prawdziwych pasjonatów, za których wszyscy podczas tej rozmowy się uważamy.
Zobaczcie
– kontynuuje Peter –
jest zupełnie inaczej, niż było jeszcze w latach 80. ubiegłego stulecia, kiedy dorastałem. Dzisiejsza młodzież nie bardzo chce rywalizować. Mają po prostu dość. Cały czas muszą mierzyć się z innymi w szkole i w życiu zawodowym. Wyścig szczurów trwa w najlepsze. Nic dziwnego, że nie chcą się ścigać ze sobą w czasie wolnym. Po drugie, pomału zanikają sporty stadionowe, do których na pewno zalicza się narciarstwo sportowe. Zamiast tego wielu aktywnych ludzi chce bliżej obcować z naturą. Rozkoszować się całymi górami, a nie tylko wydzielonymi stokami. Świat i sport zmieniają się bardzo dynamicznie.
Podczas drugiej części naszej wizyty zwiedzamy hale produkcyjne firmy Dalbello. Teraz naszym przewodnikiem jest Ivan. Najpierw oglądamy małe wtryskarki poziome, za pomocą których wytwarzane są wszystkie niewielkie elementy butów.
Wszystkie elementy z tworzyw wykonujemy sami tutaj w Asolo
– tłumaczy Ivan.
Nie możemy pozwolić sobie, żeby jakaś część niezbyt dokładnie odpowiadała naszej specyfikacji. Jeśli pęknie – dajmy na to – małe kółeczko uszczelniające zawias łączący skorupę i cholewkę, to potencjalny użytkownik nie będzie miał pretensji do naszego ewentualnego dostawcy, tylko do nas. I słusznie! Bierzemy więc odpowiedzialność od początku do końca produkcji.
Dalej podziwiamy wielkie wtryskarki pionowe, za pomocą których wykonywane są skorupy i cholewki butów. W zależności od zastosowanej technologii i materiału urządzenia te wtryskują tylko jeden rodzaj plastiku oraz w przypadku skorup szkieletowych dwa różne.
Proszę spojrzeć
– kontynuuje Ivan.
W przypadku butów dziecięcych punkt wtrysku jest z przodu skorupy, a w modelu wyczynowym na środku podeszwy. Zależy to od gęstości materiału i grubości tworzywa, które chcemy uzyskać. Takie detale muszą być za każdym razem dobrze przemyślane.
Gotowe części plastikowe wędrują na taśmę, gdzie krok po kroku buty są składane. Pracownicy (o dziwo w fabryce jest niewiele osób przyjezdnych z dalekich stron) montują kolejno inserty do klamer, składają elementy do ustawiana kątów cholewki, do środka wkładają delty, montują klamry oraz systemy ski-walk.
Wszystkie aluminiowe elementy wytwarzane są przez firmy zewnętrzne. Dostawców wyłaniamy na podstawie normalnych w takich sytuacjach przetargów. Wysyłamy projekty z określonym zapotrzebowaniem i najlepszy wygrywa. Oczywiście mamy swoich stałych dostawców, którym ufamy bardziej niż nieznanym firmom. Tak samo jest z granulatami do wtryskarek. Używamy tylko tych najlepszych
– kontynuuje Ivan.
Istotne jest, żeby granulat był bardzo suchy. Jeśli zawiera wodę, w gorącej wtryskarce zamieni się ona w parę i w gotowym produkcie wystąpią bąble. Używamy granulatów bezbarwnych i dopiero na miejscu dodajemy do nich około 1–2% tych zawierających pigmenty. Nasze wtryskarki, podobnie jak maszyny używane przez innych producentów butów, pochodzą stąd, z Asolo. W przypadku jakiejkolwiek awarii mamy zapewniony serwis w ciągu dosłownie kilku minut. To ważne, gdyż pracujemy na trzy zmiany, wytwarzając od 1600 do 2000 par butów dziennie.
Na koniec procesu, do gotowych już i kompletnych skorup wciskane są wkłady, które przyjechały z Bułgarii. Ostatni etap to kontrola jakości i pakowanie par do pudełek.
Odwiedzamy jeszcze „moldmakerów”, czyli panów odpowiedzialnych za budowę form wtryskowych. Obaj pracują w wielkim skupieniu, zupełnie jakby budowali modele maszyn latających. Ivan przedstawia nas jeszcze pani trudniącej się wytwarzaniem prototypów wkładów i rozrysowaniem szablonów. Taki wkład musi być ciepły, wygodny i stosunkowo łatwy w produkcji. Jeśli linie szwów będą biec po wymyślnych krzywych, zwiększy się ryzyko niedokładności szycia, a tego lepiej uniknąć. Zwiedzanie kończymy przy szafie z częściami do różnych modeli butów, które aktualnie znajdują się w produkcji. Na elementy te naniesiona jest siatka o powierzchni oczek 1 cm². W każdym oczku siatki napisana jest grubość materiału wzorcowego. W przypadku problemu zawsze można sprawdzić…
Wracamy do domu pełni wrażeń po tej niezwykłej wizycie. Mnie dodatkowo w uszach dźwięczą słowa Ivana:
Zobaczcie, tyle zachodu, ryzyka i inwestycji, żeby wyprodukować buty narciarskie, których cena jest często niższa niż modnych trampek lub sneakersów.
Tak, przemysł sportowy nie ma lekko…